How to plan perfect Industrial Visit
Planning the perfect industrial in-vitro validation (IV) can significantly impact a product’s quality, compliance, and performance in the industrial sector. The following guide offers a step-by-step approach to developing an effective industrial IV plan that ensures rigorous testing, high standards, and minimized risks.
Why Industrial IV Matters
Industrial IV testing involves evaluating components in a controlled environment before deployment to ensure safety, compliance, and functionality. This testing process is critical across industries such as automotive, aerospace, and pharmaceuticals, where products are expected to perform flawlessly under specific conditions.
Benefits of Industrial IV:
- Enhances Product Quality: Identifies any issues early, ensuring quality control.
- Ensures Compliance: Meets strict regulatory standards and guidelines.
- Minimizes Risks: Reduces product failure rates, ensuring reliability.
Key Considerations
- Know Your Industry Standards: Different industries follow various standards. Familiarize yourself with requirements like ISO and ASTM for effective IV planning.
- Define Testing Goals: Clear objectives help guide the testing process and provide a foundation for improvement.
Define Your Objectives and Scope
Clearly defining your objectives is crucial to a successful industrial IV process. Your objectives and scope will guide every other step, from choosing testing methods to analyzing results.
Setting Clear Objectives
Define the primary goals and expected outcomes:
- Performance Metrics: Identify key performance metrics (e.g., efficiency, durability).
- Safety and Compliance: Ensure the product meets regulatory safety standards.
- Risk Analysis: Identify potential points of failure and validate reliability.
Establishing the Scope
Define the parameters within which your testing will operate:
- Testing Types: Determine necessary tests (e.g., lifecycle, durability, stress tests).
- Environmental Conditions: Set up a controlled environment that mirrors real-world usage.
- Budget: Allocate a budget for tools, personnel, and resources needed for effective testing.
Develop a Comprehensive Testing Plan
A well-outlined testing plan ensures that every aspect of the IV process is thoroughly thought out and executable.
Choose Testing Methods and Protocols
Select the testing protocols based on your objectives:
- Accelerated Life Testing (ALT): Helps assess product durability.
- Environmental Testing: Measures product response to conditions like temperature, humidity, and vibration.
- Functional Testing: Validates that the product performs as intended.
Establish Testing Standards
Use benchmarks and industry standards (ISO, ASTM, etc.) to define success criteria:
Tolerance Levels: Set acceptable limits for each performance metric.
Comparative Analysis: Use industry standards as benchmarks to measure performance.
Create a Timeline
Plan a timeline that includes:
- Testing Phases: Outline phases for each testing type.
- Milestones: Set key performance milestones to track progress.
- Resource Allocation: Schedule resources for maximum efficiency.
Set Up the Testing Environment
The testing environment plays a pivotal role in the IV process. Trustworthy test findings require a properly regulated setting.
Calibrate and Prepare Equipment
Ensure all testing equipment is:
- Calibrated: Regular calibration ensures accurate readings.
- Maintained: Routine checks prevent unexpected breakdowns.
- Updated: Modern equipment improves test precision.
Optimize the Testing Facility
An effective testing facility setup should include:
- Sufficient Space: Ensure the facility has adequate space for equipment and safety protocols.
- Safety Measures: Install necessary safety mechanisms for high-stakes tests.
- Data Collection: Set up reliable systems to record data efficiently.
Execute the Testing Process
With everything in place, executing the IV test properly is crucial to achieving reliable results.
Best Practices for Testing Execution
To ensure consistency and accuracy:
- Follow protocols meticulously: Adhere to the testing plan to avoid data inconsistencies.
- Monitor in Real Time: Track performance in real-time to catch any anomalies early.
- Document Process: Record each stage for comprehensive data analysis later.
Quality Control Measures
Implement regular quality control (QC) to maintain standards.
- Random Sampling: Verify consistency by testing random samples.
- Peer Reviews: Have independent teams review data for objective insights.
Analyze and Interpret Data
Data analysis is where insights are derived. This step will help you understand if the product meets your quality standards and identify areas for improvement.
Data Analysis Techniques
Statistical analysis methods can help interpret results effectively.
- Descriptive Statistics: Use averages, ranges, and deviations for a quick overview.
- Failure Mode and Effects Analysis (FMEA): Determine probable reasons for failure and the effects of those causes.
- Comparative Analysis: Compare findings with industry benchmarks.
Reporting and Documentation
Documenting the results accurately is essential for implementing improvements.
- Executive Summary: Summarize key findings and insights.
- Detailed Analysis: Provide in-depth analysis with relevant graphs and charts.
Recommendations: Suggest any necessary design or protocol changes.
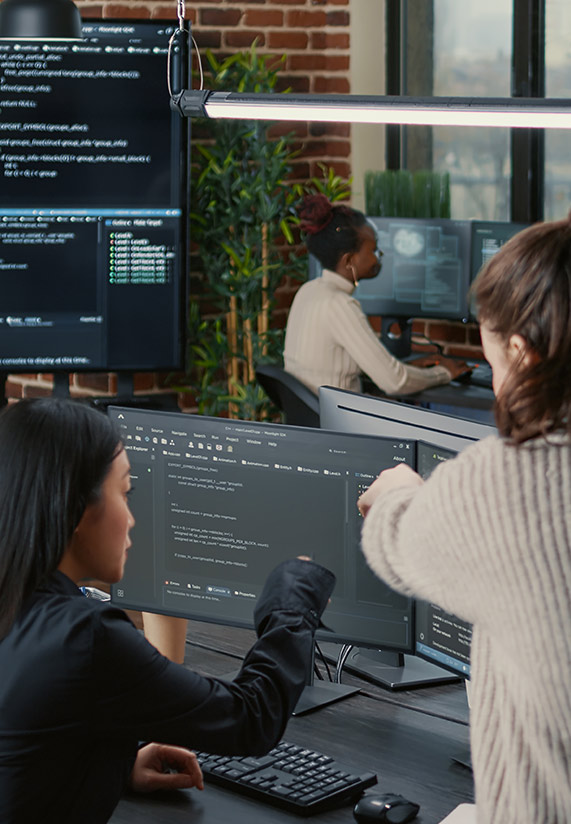
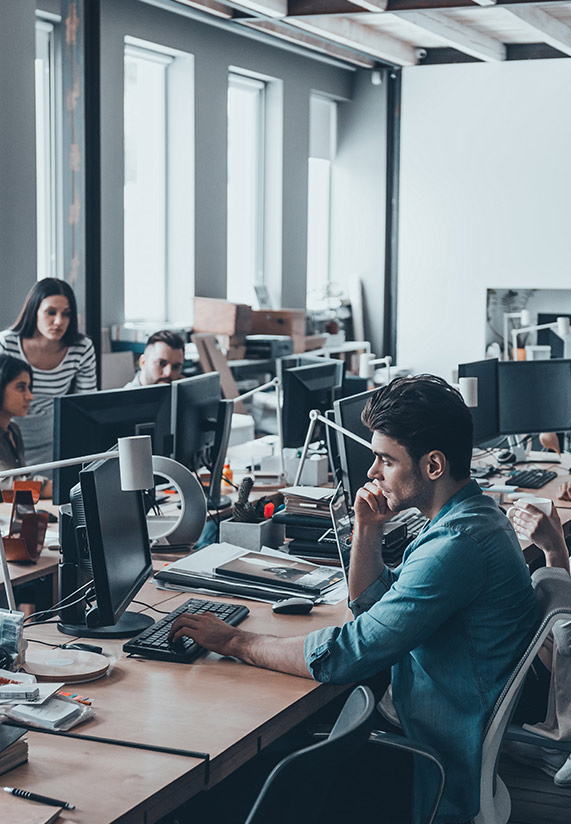

Implement Corrective Actions
The analysis often reveals improvement areas, allowing for corrective actions to enhance product quality.
Apply Changes Based on Data
The insights from the testing data should drive the following improvements:
- Product Redesign: Modify components that failed or underperformed.
- Protocol Adjustments: Update testing protocols for any missed factors.
- Documentation Updates: Document all changes to inform future testing cycles.
Continual Improvement Cycle
A commitment to improvement will refine your IV process over time, making it more efficient and reliable. Regular updates based on feedback and past testing can lead to a more effective industrial IV plan.
Common Pitfalls in Industrial IV
Planning Industrial Visit IV isn’t without challenges. Below are common pitfalls and strategies to address them.
Pitfall 1: Budget Constraints
Industrial IV can be resource-intensive. To manage costs:
- Prioritize high-risk areas: Focus on testing areas that carry the most significant risk.
- Use automated solutions: Automation can reduce labor and improve repeatability.
Pitfall 2: Data Management:
Large datasets from IV testing can be challenging to handle.
- Use cloud-based storage: cloud storage simplifies data access and analysis.
- Data Backup Protocols: Regularly back up data to prevent loss.
Pitfall 3: Inconsistent Test Results
Inconsistent results can undermine the validity of your tests.
- Regular Calibration: Maintain equipment to ensure consistent readings.
- Cross-Verify Results: Use multiple testing methods for critical areas.
Conclusion
Planning the perfect industrial IV requires clear objectives, structured testing plans, a controlled environment, accurate data analysis, and the implementation of insights. By following these guidelines, you’ll achieve a validation process that enhances product quality and compliance while reducing risks.
Zoople Technologies stands out as a top software training institute, offering high-quality courses supported by an MNC-backed company. With expert trainers, hands-on learning, and industry-relevant skills, Zoople Technologies ensures students are well-prepared for successful careers in technology.